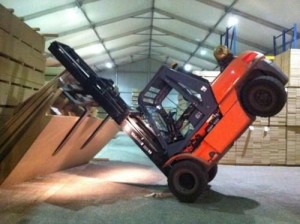
This is why the load center is important and needs to be understood.
To understand the concept of load center, visualize two children – one bigger, one smaller – on a playground see saw. Because of his weight, the bigger child will control the see saw; however, if the smaller child moves farther back on the seat and leans back, she will gain leverage and have more control. A counterbalance lift truck is basically an industrial see saw that can be driven. The lift truck is the “bigger child” and the load is the “smaller child.”
Two dimensions have an effect on leverage. Dimension A is determined by the manufacturer based on engineering standards and does not affect load center. The front axle is the pivot point for the forklift. The farther away the upright face of the fork or attachment from the centerline of the axle, the less lifting capacity the forklift will have. When an attachment is added, the weight and increased distance from the centerline of the front axle to the new load is considered. If Dimension A is changed the manufacturer must be involved with the revision of the forklift’s capacity rating for its data tag.
Dimension B is the load center rating of the truck and is based on the standardized U.S. load size of a 48×48” cube. The center of the cube would be 24” out from the upright face of the forks and 24” up from the horizontal face of the forks.
When training operators on a forklift’s load center and stability, he or she must understand:
- When a load is larger than the standard, lifting it can have an adverse affect on stability
- Every inch of extended load center may cause the load to feel 100 lbs heavier
Because every load is unique, each one must be evaluated individually by the operator; however, if loads outside of the standard are transported on a regular basis, a manufacturer can assist with providing an alternate load center rating for your application.