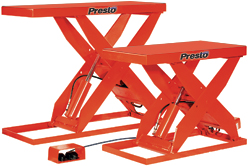
Lift tables are used to raise and position workpieces for ergonomic access. They are used for material positioning, load positioning, or lifting in applications such as construction, automotive and garage service, electrical and power service, telecommunications, manufacturing, and inventory management. Lift tables are also used in the wire and cable industries and in other applications, such as painting, where access to above ground locations is required. Important specifications for lift tables include lift capacity, vertical lift travel, platform width, platform length, and actuation method. Lift capacity is the maximum force or load supported by the lift. Vertical lift travel describes the difference between fully lowered and fully raised lift positions. Platform width is the narrow dimension of the lift platform. Platform length is the long dimension of the lift platform. Lift tables may be actuated by hand cranks, screw drives, foot pumping and ratcheting, pneumatic air cylinders and air motors, hydraulic cylinders and motors, or electrical motors.
There are a number of mechanisms by which industrial lift tables may be raised or lowered. These include scissor lifts, screw lifts, rack and pinion lifts, telescoping lifts and articulated lifts. Scissor lifts use linked, folding support members to achieve lifts. The lifting action occurs when the members are drawn together, typically with a screw mechanism. Screw lifts employ the mechanical advantage of threads to lift a workpiece vertically. Rack and pinion lifts function via a small drive gear (pinion) that drives a straight-toothed rack to lift the load. The telescoping lift mechanism has multiple sections that retract and extend into and out of each other. Articulated lifts have multiple sections that unfold or articulate to lift a platform or bucket. Frequently, cherry pickers are articulated lifts.
Features common to lift tables include tilting, rotating, counterbalance, wheels, hand or safety rails and truck mounting. Lift tables may have tilting and rotating functions in addition to lifting. A counterbalance is a weight feature on load lifts to prevent lift overturning without relying on legs or supports under the load. They may also come equipped with wheels to provide rolling for load transport and positioning; typically equipped with a brake or stabilizing outriggers. Hand and safety rails provide for personnel safety or to prevent load from falling or sliding off the lift.